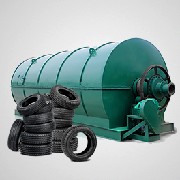
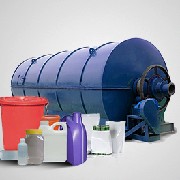
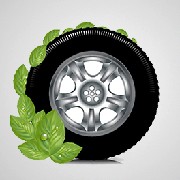
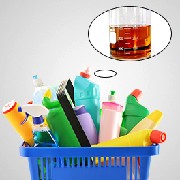
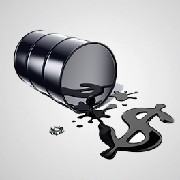
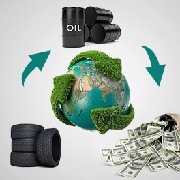
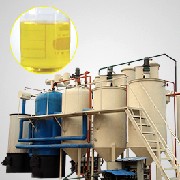
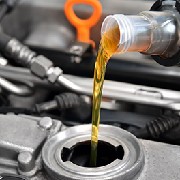
The method of extracting crude oil from waste tyres is mainly to use thermal pyrolysis plant, an environmentally tyre recycling machine, placing waste tyres in industrial low temperature, slightly positive pressure, oxygen-free environment, and using heat energy to crack waste tyres from high molecular weight substances into low molecular weight substances such as tyre crude oil (tire pyrolysis oil/TDF tire derived fuel), carbon black, and tail gas.
The waste tyre to crude oil making process mainly includes five sections: feeding, pyrolysis, condensation, slag discharge, and flue gas treatment. Here is a 3D video that displays the waste tyre to crude oil making process:
Feeding Section: First, the waste tyres are put into the tyre pyrolysis plant reactor and seal the doors in the reactor. Batch waste tyre pyrolysis plant uses a manually controlled grabber and a hydraulic automatic feeder to directly squeeze the waste tyre raw materials into the pyrolysis reactor. The feeding method of semi-continuous tyre pyrolysis plant and fully continuous tyre pyrolysis plant is auger feeding, so the waste tyres need to be crushed and ground into rubber powder, and then transported to the tyre pyrolysis reactor through the feeding auger.
Different feeding ways for waste tyre pyrolysis process
Pyrolysis Section: After waste tyres or rubber powder are transported to the pyrolysis furnace, the burner is turned on, and pyrolysis reactor will rotate and be heated. According to the needs, indirect heating or direct heating can be selected. Fuel oil, gas, coal or wood can be used as heating fuel. When the inside temperature reaches the degree of 250 to 280, the oil gas will begin to generate while flow through oil gas separator, and continuously produce until the temperature up to the degree of 300 to 450. After tyre pyrolysis machine produces crude oil, gas and syn-gas, the syn-gas can be treated and used as heating fuel for tyre pyrolysis furnace.
Direct and indirect heating way for tyre pyrolysis reactor
Condensation Section: in oil gas separator, light component will enter the condensers, meanwhile, heavy component will be liquefied into tyre pyrolysis crude oil and then automatically discharged into heavy oil tank. A small amount of oil gas cannot be liquefied and will be transferred by water seal tank back to the burning. There are two common condensation systems: shell and tube condensation system and water tank condensation system.
Waste tyre pyrolysis oil cooling system
Slag Discharge Section: In addition to oil and gas, the tyre pyrolysis reaction will also produce a part of carbon black. After cooling, the batch waste tyre pyrolysis plant can be discharged by front slag discharge or rear slag discharge, and directly sold or further processed. While the semi-continuous and fully continuous tyre pyrolysis plants use the slag discharge auger to achieve high-temperature continuous slag discharge.
Flue Gas Treatment Section: The flue gas produced by the reactor heating must be treated by environmental protection equipment to remove pollutants such as sulfides, nitrogen oxides, and particulate matter in the flue gas, and meet the national and regional standards for qualified emissions.
Environmental devices of waste tyre pyrolysis plant
The above is the process flow of making crude oil from waste tyres through the thermal pyrolysis technology. If you also want to convert waste tyres into wealth, please feel free to contact Henan Doing Company for suitable scale waste tyre pyrolysis plants and professional technical services.